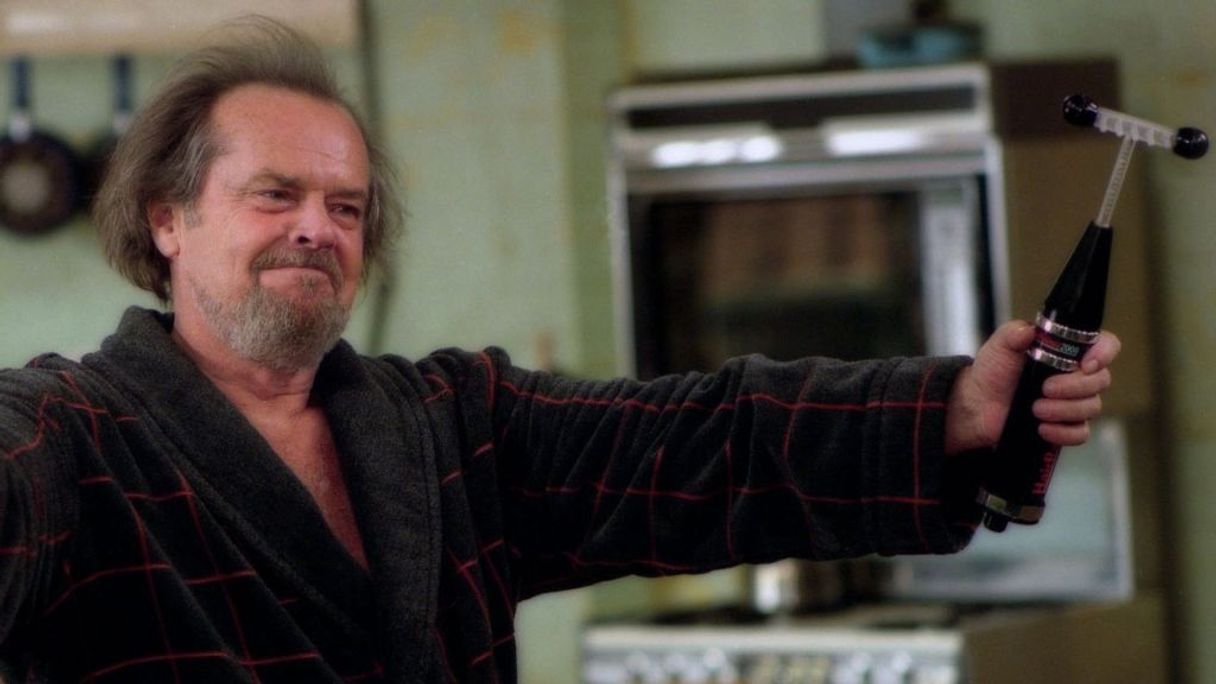
Best Practices for AI-Enhanced Inventory Management
Ina Rudziankova for Academy
Best Practices for AI-Enhanced Inventory Management
Managing inventory for your repair service business can often feel like a balancing act. From keeping track of parts across multiple locations to ensuring that popular items are always in stock, the complexity can be daunting. But what if there was a way to simplify the entire process and enhance efficiency simultaneously?
Enter Artificial Intelligence. Integrating AI into your inventory management can transform a hectic workflow into a streamlined operation. Here's how AI can make inventory management nearly effortless:
Simplified Multi-Location Management
AI integrates all your inventory data, providing a unified and transparent view of stock levels whether they’re in your shop, warehouse, or online store. This clear oversight helps you manage supplies effectively without the usual hassle.
Efficient Order Processing
AI automates routine tasks such as generating purchase orders and monitoring stock, which frees up your time to concentrate on growing your business. This means less time spent on mundane tasks and more on strategic planning and customer service.
Enhanced Customer Satisfaction
By predicting demand more accurately, AI ensures you have the right parts available when needed, preventing stockouts and ensuring a smooth customer experience. Satisfied customers are likely to return, boosting your business's reputation and sales.

Key Benefits of AI in Inventory Management
The transition to AI-driven inventory management is not just about reducing stress — it's about leveraging technology to make substantial improvements:
Increased Accuracy
Unlike traditional methods that may rely on guesswork, AI analyzes extensive data sets — including past sales, market trends, and even social media insights — to forecast demand with impressive precision. Here’s what this accuracy means for you:
- Reduced Excess Stock: A McKinsey study shows that a successful AI-powered inventory management implementation can reduce inventory levels by 35%, ensuring your warehouse contains fewer products that customers aren’t interested in.
- Prevention of Overstocking: AI identifies potential surplus before it becomes an issue, helping you save on storage costs and avoid unnecessary overstock.
Boosted Efficiency
AI not only predicts demand more accurately but also automates the creation of purchase orders and continuous stock monitoring. This automation shifts your focus from repetitive tasks to areas like marketing and customer relationship building.
- Demand Forecasting: AI takes the guesswork out of predicting demand, freeing your team to focus on more strategic initiatives.
- Generating Purchase Orders: AI can analyze data and automatically generate purchase orders to maintain optimal stock levels. No more manual calculations or wasted time!
- Inventory Level Tracking: AI keeps a constant eye on your inventory levels, eliminating the need for manual checks and spreadsheets.
Cost Reduction
The precision and efficiency of AI have a direct positive impact on your finances by:
- Lowering Inventory Costs: Minimizing surplus stock reduces storage and insurance costs.
- Decreasing Storage Expenses: With better stock management, you might even reduce the amount of storage space you need, cutting costs further.
- Streamlining Order Processing: Faster processing with automated systems can lower labor costs.
Improved Client Relations
The ultimate advantage of AI-enhanced inventory management is the improvement in customer satisfaction. Efficient operations ensure that clients receive what they need promptly, enhancing their overall experience and potentially increasing loyalty.
Embracing AI for your repair service inventory management doesn't just simplify operations — it strategically advances your business in a competitive market.

How AI Streamlines Inventory Management
AI-enhanced inventory management simplifies complex tasks by transforming raw data into actionable insights. Here's a closer look at how it works in the context of repair services:
Data Collection
AI systems act like comprehensive sensors that capture and consolidate data from multiple sources that influence your repair service operations. This data includes:
- Sales History: By analyzing past sales, AI helps you understand demand trends for different services or parts.
- Point-of-Sale Systems: Real-time data from your POS systems offers immediate insights into which parts or services are in demand, helping adjust your inventory accordingly.
- Marketing Data: AI examines how your promotions and advertising campaigns affect sales, enabling more precise marketing strategies.
- Competitor Analysis: Observing your competitors’ activities can provide foresight into market trends and help you prepare for shifts in consumer preferences.
Data Analysis
After gathering the data, AI uses advanced algorithms to sift through and analyze these vast datasets. This analysis might uncover:
- Seasonal Trends: Showing when certain repairs are most in demand.
- Effects of Marketing Efforts: On specific parts or services.
- Emerging Trends: In consumer behavior or new technologies affecting service requirements, supporting personalized product discovery by identifying which parts or services individual customers are likely to seek.
Demand Forecasting
With these insights, AI accurately predicts future demand for your services and parts. This foresight allows you to optimize inventory levels — ensuring you have the necessary items on hand without overstocking.
Task Automation
Beyond forecasting, AI automates several inventory management tasks, making operations more efficient:
- Automatic Purchase Orders: AI predicts when stock will deplete and automatically places orders to replenish inventory at the ideal time.
- Inventory Optimization: Continual monitoring of stock levels, coupled with supplier lead times, enables AI to adjust inventory dynamically, avoiding shortages and excess.
- Reorder Alerts: AI proactively sends notifications when it's time to reorder stock, ensuring you never run out of crucial items.
This approach not only enhances operational efficiency but also significantly improves customer satisfaction by ensuring parts and services are always available.

Best Practices for AI Integration in Inventory Management
To successfully integrate AI into your inventory management, consider these steps:
Start with a Pilot Project
Testing AI through a pilot project helps you understand its impact in a controlled environment. Here’s how to initiate this process:
- Select a Focus Area: Choose a particular service line or a specific location to implement AI. Ensure the data is clean and the operations are representative of your broader business.
- Set Clear Objectives: Determine what you aim to achieve with the pilot, such as reducing delays in service delivery or optimizing parts inventory.
- Prepare Your Data: Accuracy in data is critical for AI's effectiveness. Ensure all data inputs are current and comprehensive.
- Select an AI Solution: Choose a solution that meets the specific needs identified during your planning phase. Factors to consider include the solution's capability to integrate with existing systems, its ease of use, and scalability.
- Implement and Monitor: Deploy the AI system and monitor its performance against your objectives. Key performance indicators might include improvement in service speed, reduction in stockouts, or better inventory turnover.
- Evaluate and Adjust: After the pilot, evaluate the outcomes and refine your approach as necessary. This might involve adjusting AI parameters, improving data quality, or expanding the scope of AI utilization.
Choosing the Right AI Solution
Selecting the optimal AI tool involves several key considerations:
- Needs Assessment: Identify the most critical areas for improvement within your inventory management processes.
- Stakeholder Input: Gather feedback from team members who will interact with the AI system, including technicians, inventory managers, and customer service staff.
- Vendor Selection Criteria:
- Data Capability: Can the AI handle the scale and complexity of your data?
- Accuracy and Optimization: Does it provide precise forecasts and optimize inventory efficiently?
- Integration and Scalability: Ensure the AI solution can grow with your business and integrate smoothly with existing systems.
- Cost vs. ROI: Consider whether the investment in AI will deliver tangible returns through reduced costs and enhanced efficiency.
- Support and Training: Availability of training and ongoing support from the vendor is crucial for successful implementation.
Implementing AI in your inventory management can revolutionize how you manage stock and respond to customer needs, making your repair service more efficient and responsive.

Optimizing Your Inventory Management: Cleaning Data for AI Integration
In the world of inventory management, data quality is paramount. Poor data can undermine the effectiveness of AI-driven systems. Common issues include:
- Inaccurate Data and Analysis: Mistakes in data collection or flawed analysis can mislead demand forecasting, leading to insufficient or excessive stock levels.
- Erroneous Data Entry: Manual data entry is prone to human error, leading to inconsistencies that can skew your understanding of inventory levels.
- Lack of Data Transparency: Without seamless integration with Enterprise Resource Planning (ERP) systems, it becomes challenging to efficiently manage orders and track product locations.
- Delayed Inventory Counts: Infrequent checks can exacerbate discrepancies between actual stock and system records, complicating error resolution.
- Disorganized Data Storage: A cluttered warehouse with mislabeled items or poorly arranged stock can lead to operational inefficiencies and data inaccuracies.
- Lack of Data Backup: Ensuring regular data backups, particularly in cloud environments, is crucial for safeguarding your inventory information against hardware failures.
Implementing Data Hygiene Practices
To tackle these challenges and prepare your data for AI integration, consider the following practices:
- Standardize Data Entry: Adopt consistent protocols for data entry, such as using barcode scanners or automated systems, to minimize human error.
- Conduct Regular Inventory Audits: Periodic physical counts help verify data accuracy and address discrepancies.
- Set Data Validation Rules: Implement rules in your systems to automatically detect and correct entry errors, ensuring data integrity.
- Integrate Systems: Ensure your inventory management system works in harmony with other business systems (like ERP or CRM) to maintain consistent data across all platforms.
- Remove Duplicates: Regularly cleanse your database of duplicate entries to maintain accurate inventory levels.
- Archive Data Strategically: Employ a data archiving strategy to manage historical data, keeping active inventory records streamlined and manageable.
Tools for Data Cleansing
Several tools are available to assist in maintaining pristine inventory data:
- OpenRefine: A robust, open-source tool that offers extensive data cleaning capabilities.
- Syncari: A cloud-based solution designed to facilitate data cleansing and integration for businesses.
- Trifacta Wrangler: An enterprise-grade tool providing powerful data transformation and cleaning features suitable for large datasets.

Integrating AI Inventory Management into Your Business
To fully leverage AI in inventory management, follow these steps:
- Assessment and Planning: Review your existing processes to pinpoint improvement opportunities. Assess each AI tool’s compatibility with your infrastructure, focusing on API integration and customization possibilities.
- Vendor Selection: Choose a vendor that matches your specific needs, considering scalability, integration ease, support quality, and cost-effectiveness.
- Integration Process: Work with your chosen vendor to implement a pilot project, which will help gauge the tool's effectiveness on a smaller scale before wider application.
- Data Preparation: Cleanse and organize your data to ensure it is accurate and consistent, setting a solid foundation for AI analysis.
- System Configuration and Customization: Tailor the AI tool to meet your specific inventory demands, such as adjusting demand forecasting settings and customizing dashboards for better visibility.
- Testing and Optimization: Monitor the system’s performance and make necessary adjustments to optimize its effectiveness.
- Training and Adoption: Educate your team on using the new system, emphasizing the benefits of AI-driven insights for smarter decision-making.

Key Insights and Impact of AI in Inventory Management
Transformative Impact on E-Commerce
The incorporation of AI in inventory management is revolutionizing the e-commerce sector, significantly enhancing operational efficiencies and customer experiences. Here are some notable impacts:
- Reduction in Stockouts: A 2023 study by Myos on inventory management highlights that AI implementations can decrease stockouts by up to 50%. This significant reduction not only leads to happier customers but also minimizes lost sales opportunities, bolstering brand reputation.
- Enhanced Inventory Turnover: Companies that have integrated AI report an average improvement of 20% in inventory turnover rates. This metric indicates a more strategic use of storage space and capital, fostering greater business profitability.
- Boosted Order Processing Efficiency: AI excels in automating repetitive tasks such as order picking and packing, which translates to an average reduction in order processing times by 15%. This efficiency is crucial for scaling operations and improving overall workflow in warehouses.
Visualizing the Benefits
Consider a graphical representation showing inventory carrying costs over time. A traditional management approach might show a flat line, indicating steady costs. In contrast, an AI-enhanced approach would display a downward slope, illustrating significant cost reductions due to optimized stock levels and reduced overstocking.
Benchmarks for Strategic Comparison
Understanding how your business compares to industry standards can be incredibly beneficial. Here are some key metrics to consider:
- Inventory Turnover Rate: This metric measures the efficiency of selling and replacing inventory within a given period. It’s calculated by dividing the cost of goods sold (COGS) by the average inventory level. Typically, a higher rate indicates efficient inventory management, translating to reduced storage costs and better capital utilization. Industry standards suggest a healthy turnover rate ranges between 4 and 8, but AI can push these boundaries further by enabling real-time data-driven stock optimization.
- Order Fulfillment Accuracy: According to the 2023 Customer Service Benchmark Report by BenchmarkPortal, the industry average for order fulfillment accuracy stands at about 95%. AI can help surpass this benchmark by reducing manual errors and providing precise real-time stock updates, ensuring higher accuracy in order fulfillment.
- Labor Cost Reductions: Labor costs, which constitute approximately 65% of total warehouse operating expenses, can be significantly impacted by AI. Automation of tasks like order picking reduces the need for extensive manpower, allowing staff to focus on more strategic roles, thus potentially decreasing overall labor costs.
Embracing AI in inventory management offers e-commerce businesses an opportunity to excel in efficiency, accuracy, and customer satisfaction. This guide provides the essential steps and considerations for integrating AI effectively, from selecting the right tools to preparing data and ensuring smooth operation. Remember, the successful deployment of AI not only improves operational capacities but also sets a foundation for sustained growth and customer delight.
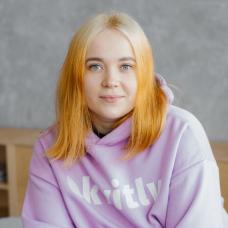
Ina Rudziankova
Product Marketing Manager. Loves parrots and cats.
Are you ready?
Explore 🌱kvitly with no limits within the trial period of 14 days. No commitment, no credit card required.
Let’s try!